202341 - No inert gas means less tanker safety
A chemical tanker was in port to unload a cargo of heptene, a highly flammable chemical liquid. First, the loaded tanks were partially drained to check the piping, pumps and valves for leaks.
As edited from Dutch Safety Board Report Summary July-December 2022
Then the forward cargo tanks (1 starboard and port) were completely unloaded. When these were empty, the cargo pumps of tanks three port and starboard were started and the piping system of the forward tanks was disconnected from the central discharge line to shore.
There was still residual cargo in the discharge lines of the forward tanks. To remove this residual cargo, the lines were to be blown with compressed air at 8 bar. This would force the cargo through the central discharge line and the stripping line from the forward cargo tanks into tank 5S. A drain valve used to take samples was connected via a flexible hose (and Y-joint) to the drain valve. The Y-joint was then attached to the vapour lock connection on tank 5S. In this way, residual cargo from the discharge lines would be collected in tank 5S, which would be the last to be discharged. This method had been used with success by the crew for many years, although it was not strictly in line with the company’s written procedure.
Seconds after the compressed air was blown into the discharge line, an explosion occurred. The investigation was able to discount a pressurisation event as the cause. In all likelihood, an explosive mixture ignited in tank 5S due to static electricity. No inert gas or closed vapour return system had been used when loading this cargo. During the first outflow of cargo (safety ullage), outside air was drawn in through the pressure/vacuum valve. This allowed an explosive mixture of gas vapours and oxygen to develop in tank 5S The official investigation found that maximum safety assurance can only be achieved by inert loading or loading with a closed vapour return system. Ships without these systems should therefore no longer be allowed.
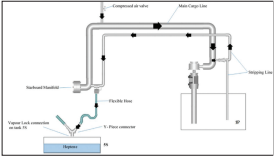
Lessons learned
This was another case of not following procedures, as in MARS 202340 and MARS 202343, among others. Although in this case the deviation from the procedure probably did not contribute to the explosion, it is an indicator of poor safety culture.
In 2017, the OCIMF cited an analysis of 35 incidents (over 25 years) compiled by an inter-industry working group that reported to IMO. This analysis showed that:
- In the majority of cases the ship was tank cleaning, venting or gas freeing when the incidents occurred.
- Failure to follow established procedures was observed in a significant number of incidents.
- In several cases, the tank atmosphere for tanks without inert gas had apparently not been evaluated or was not being monitored.
- In most cases ignition occurred within a cargo tank.
- None of the incidents occurred during the use or operation of inert gas