201107 Capsize of vessels carrying nickel ore, with fatalities
Condensed from BIMCO News 12 Nov 2010, UK P&I Club LP Bulletin 602, Nepia Signals no. 69
Recently, two bulk carriers loaded with Indonesian nickel ore (sometimes also known as nickel laterite, lateritic nickel ore, limonite or saprolite, and usually shipped from Indonesia and the Philippines) sank at sea with fatalities.
The standard methods of determining the flow moisture point (FMP) of bulk cargoes which may liquefy, as stated in the International Maritime Solid Bulk Cargoes Code (IMSBC), were developed primarily for homogenised metal concentrates, whereas nickel ore is a mixture of very fine clay-like particles and larger rock particles of various sizes. Moreover, metal concentrates have a typical moisture content of about 10 per cent, whereas nickel ore often has a moisture content in the range of 25-40 per cent. These problems make it difficult to test nickel ore for liquefaction parameters.
Serious doubts have been expressed about the accuracy of transportable moisture limit (TML) and moisture content (MC) data that is provided to masters at nickel ore loading ports. In many instances, the sampling and testing is carried out by the mine's in-house laboratory and the certificates only state that the material has been tested in accordance with the IMSBC flow table test (FTT) method and found to pass. No figures for the FMP and TML are stated although average MC, which is valueless without a TML, is provided. Furthermore, audits of the sampling and testing methods used by these mines have always revealed serious deficiencies, making values certified by shippers meaningless.
If the 'can test' performed by the vessel's crew indicates the likelihood of moisture migration and liquefaction, the cargo as a whole must be assumed to be unsafe for carriage regardless of shippers' certification. In many cases of Appendix A cargoes Ð those that are liable to liquefy Ð shipowners are faced with a choice of either accepting the values certified by shippers knowing that they may be unreliable, or of becoming involved in a costly investigation and possible rejection of the cargo with its attendant legal consequences. These actions are beyond the expertise and capacity of the master and an ordinary cargo surveyor and only expert attendance at the mine and in port can properly conduct the sampling and certification procedures necessary to ensure the safety of cargo, crew and vessel.
In a recent case, it was found that the mine, in clear violation of the IMSBC, did not routinely sample the stockpiles prior to shipment, but rather the sampling was conducted during the course of loading. This data was then presented to the master of the next vessel to load at the terminal. In turn, the results of the analysis of the cargo loaded on board the subject vessel would then be presented to the next ship and so on. Due to this illegal practice, the master would have been totally unaware of the fact that he was carrying a cargo for which the documentation was deliberately false, and that despite acceptable parameters on the certificate, the cargo could very well liquefy and potentially capsize the vessel.
The interval between sampling/testing and loading must never be more than seven days. If the cargo has been exposed to significant rain or some form of moisture between the times of testing and loading, further tests shall be conducted to ensure that the MC is still less than the cargo's TML, which is generally determined as 90 per cent of FMP.
Mariners must remember the simple relationship MC < TML < FMP. Only if the MC is significantly less than the TML can the cargo be considered to be safe to load. It is also important not to confuse the commercial MC with FMP. Even though a receiver may be willing to accept cargo with a MC of 35 per cent by weight, it can only be accepted by the vessel if this is well below TML.
In the laboratory, the FMP is determined by adding water to a stock sample of nickel ore until a flow state is determined. The FTT method involves preparing a sample on a flow table in the form of a truncated cone. The flow table top is then raised and allowed to fall sharply through a defined vertical distance. This simple procedure is repeated up to 50 times and the behaviour of the sample cone observed to see if 'plastic deformation' has occurred. However, the IMSBC states that the method may 'not give satisfactory results for some materials with high clay content', which means that great care is required in performing the test for nickel ore.
Appendix 2 of the IMSBC Code (2009) states: 'A flow state is considered to have been reached when the moisture content and compaction of the sample produce a level of saturation such that plastic deformation occurs. At this stage, the moulded sides of the sample may deform, giving a convex or concave profile'.
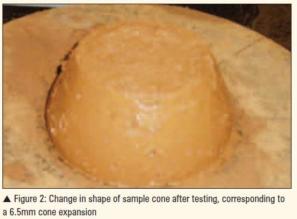
Figure 1 illustrates the shape of a sample cone for a sample below FMP, while Figure 2 shows the shape of a sample cone after recent testing with a MC of about 31 per cent. Despite the cone being deformed, with a recorded cone expansion >6mm, it was regarded as being below FMP.
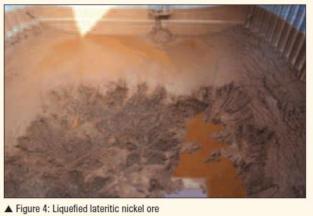
The sample was not failed until the cone had expanded by a massive 20mm, as shown in Figure 3, with a declared FMP of 33.8 per cent. The mine was unable to justify their change of methodology, which ignored all the key indicators of a flow state (see page 300 of the IMSBC Code: Editor), and enabled them to ship wetter cargo at a greater risk to the vessel.