201024 Hand injury during crane maintenance - with FEEDBACK in Dec 2010
Hand injury during crane maintenance
- with FEEDBACK in Dec 2010
MARS Report 201024
On a tanker in port, a leading seaman’s right hand was injured during an attempt to remove the sheave axle (pin) from the port hose crane jib head block. The work involved the renewal of a bearing on the port hose crane sheave to ensure free movement of this critical component. The same task had been successfully completed the previous day by the same team on another crane.
Before starting the work, the chief engineer, leading seaman and a cadet completed a toolbox talk on the intended operation, including a discussion on the use of a hydraulic jack designed to draw out the pin.
The following documentation was also completed for the work planned:
Toolbox meeting;
Working aloft permit general;
Lock-out permit for the main breaker on the port hose handling crane.
The necessary scaffolding had been erected earlier under the supervision of the leading seaman. After completing an inspection of the scaffolding, the chief engineer and leading seaman proceeded to climb it and began the work. Both were properly fitted with appropriate personal protective equipment (PPE), including approved full body harnesses and fall arrest equipment. The cadet remained on the deck, serving as a helper. The first step in the work process included tying off the crane wire to reduce the load on the sheave.
In order to remove the sheave pin, a length of threaded rod was screwed into a bore at the end of the pin. The free end of the rod was passed through a hollow pipe section and the annular hole of the jack’s piston and then secured with a nut. As pressure was built up in the jack, a pulling force was applied to the sheave pin. The force applied was registered on a pressure gauge in bar. An initial pulling force of approximately 250 bar was applied to the pin. To assist the applied force, the chief engineer tapped the free end of the pin with an 8 lb maul. To prevent damage to the pin end, the leading seaman held a heavy brass stock between the pin and maul.
The chief engineer initially applied three blows with the maul, resulting in a pressure drop indicating movement in the pin. Again the hydraulic jack was pumped to approximately 250 bar pressure, the pin was struck again and the deflected maul landed heavily on the leading seaman’s right hand. He immediately descended the scaffolding with the assistance of the chief engineer. On reaching the deck atop of the midship store, additional crew members were available to assist him to the ship’s hospital.
The vessel’s captain immediately arranged transport to the hospital ashore for medical attention. There, X-rays determined a fracture in the upper right hand and the casualty was repatriated for treatment and recovery.
Result of investigation
1. Weak assessment of the risk associated with swinging an 8lb hammer in close proximity to a co-worker’s hand.
2. The leading seaman indicated he heard a slight ‘click’ prior to the maul making contact with his hand, and suspects the handle of the maul struck the crane wires, thus causing the maul blow to deflect off the stock.
Root cause/contributory factors
1. Failure to follow procedures. There was no evidence of a proper risk assessment for the intended work. A risk assessment must identify all hazards associated with the work;
2. Failure to warn. Both individuals failed to identify the ‘line of fire’ issue with swinging a maul in very close proximity to an unprotected hand and the potential for injury;
3. The fact that the same job had been completed on another crane the previous day without incident seemed to give a false sense of safety on the day of the incident. This is often a common thread in many serious accidents;
4. There was evidence from a post incident interview that the crew members felt that time devoted to completing a formal risk assessment would have consumed valuable maintenance time. This indicated an improper assessment of priorities.

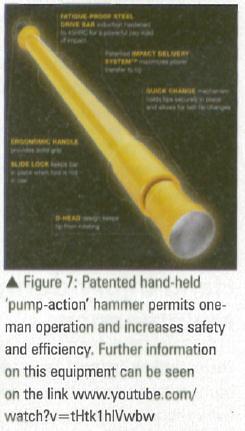
Corrective/preventative actions
1. Incident report circulated throughout the fleet.
2. Decision taken to expedite the implementation of a work safety training programme in the fleet.
3. New procedure adopted for ships’ safety officers to ensure supervision of ships’ crew during major onboard maintenance tasks. This will include attending daily work planning, toolbox meetings and assisting with risk assessments.
4. Company’s standard toolbox meeting form to include a system of ‘hazard hints’ to assist crew in identifying hazards in their daily work routines.
5. Shore staff attending the vessel during major projects shall review the daily work planning and provide oversight and input to ensure safe operations on board.
6. Share findings of this report with the industry.
7. Issue company safety bulletins to create awareness of safer hand tools.
Editor’s Note: Although the arrangement for extracting the sheave pin appears to be in order, the risk assessment must consider the possibility of two more hazards when applying tension with the hydraulic jack; 1) the rod coming off the the pin due to corroded / wasted threads, and, 2) the threaded rod fracturing, especially if not of approved strength or part of original manufacturer’s kit. In both cases, the separate components (bolt, jack and supporting pipe) are certain to be projected with great force and represent a injury hazard to crewmembers, and if the vessel is a tanker, a spark ignition hazard under certain conditions. It is suggested that a shroud made of strong canvas should be rigged to cover the rod at the free end and also pass underneath to entire length of the apparatus to prevent the components falling on the deck.
FEEDBACK published in December 2010 issue of Seaways: The resulting injury noted in this report is highly unlikely to have been avoided by the corrective/preventative actions described. While I agree with these actions, surely a heavy hammer coming into accidental contact with an unprotected hand will not be prevented by any number of risk assessments, hazard hints or planning, except the use of a suitable tool to hold the stock which the seaman held? Once again, it seems that everyone is trying to eliminate risk completely which surely in never going to be achievable?
Editor's note: Had a proper risk assessment (a commonly used technique is illustrated in the MCA publication Code of Safe Working Practices) and a tool box meeting been conducted before commencing the task, one of the hazards identified would have been that of a 'heavy hammer coming in accidental contact with an unprotected hand'. Consequently, the person in charge would have been compelled to take appropriate control measures, as in this case, both the quantum of risk (heavy hammer striking hand) and the severity of such a strike (serious injury) would have been unacceptably high. While it is true that risk can never be eliminated completely in many cases, the goal should be to reduce risk to 'as low as reasonably practicable' (ALARP), ideally to a tolerable or negligible level. It is always prudent for ship's crews to preserve evidence of having conducted proper risk assessment and this is already a requirement under most international/national safety regulations, industry guidelines, P&I club advice and company procedures.