200954 Fatality due to asphyxiation
Fatality due to asphyxiation
MARS Report 200954
Fearing possible liquefaction of the copper concentrate, a group A cargo in the BC Code which can liquefy if moisture content nears transportable moisture limit (TML), the chief officer of a bulk carrier decided to get the ship's deck cadet to enter no. 1 hold from the forward access, to view and report on the state of the cargo. Upon opening the hold access located in the fore peak store, the officer reportedly instructed the cadet to prepare portable lighting while he himself went to get a self-contained breathing apparatus (SCBA) set. Unsupervised, the cadet apparently entered the hold wearing a heavy-duty dust mask which he could have mistaken for an emergency escape breathing device (EEBD). After reaching the top landing platform of the hold ladder, four metres below the upper deck, he collapsed and lost consciousness.
Almost 15 minutes were lost before a properly equipped rescue attempt could be made by persons wearing SCBA, and all efforts to revive the cadet proved unsuccessful.
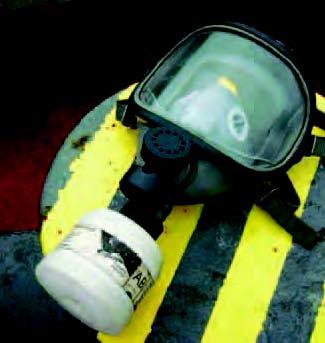
an EEBD. Such masks should be clearly marked ‘Not for use in oxygendeficient
atmosphere’ in a language understood by the crew
In-house investigation findings
Safety management system procedures for entry into enclosed space were not followed.
The access trunk had not been ventilated and tested for oxygen or toxic gases.
The enclosed space checklist had not been completed.
There was no strategy, planning or briefing carried out before proceeding to attempt to enter the hold.
There was a lack of skill in dealing with an emergency situation: the crew took too long to launch a rescue operation.
Subsequent measurements at the top landing platform showed an oxygen concentration of 3.2 to 4.4 per cent: certain to result in instantaneous asphyxiation.
Corrective actions
Entry into loaded cargo holds with main hatch covers closed is prohibited at all times other than in an extreme emergency. This is applicable for all cargoes at all times: many bulk cargoes have the potential to deplete oxygen or to emit poisonous and or explosive gases.
If entry into an enclosed space is unavoidable because of an emergency situation, an SCBA must be used by the person making entry.
Cadets on board are trainees, under the supervision and observation of senior officers. They are not to be assigned jobs of a hazardous nature under any circumstances.
Mast houses or store spaces which have booby hatch access to cargo holds must also be treated as confined spaces on loaded passages.
Tests for oxygen content in an enclosed space must be attempted only after good ventilation with an instrument capable of testing the atmosphere from outside the space.
A pre-loading cargo meeting must be conducted onboard and all crew members informed of the hazards associated with the cargo being loaded. Material safety data sheets (MSDS) for the cargo should be obtained from shippers.
Any dust/gas masks available on board must be clearly identified and labelled in languages understood by the crew detailing their limitations and with 'not to be used in oxygen deficient atmosphere' on them.
Risk assessment and detailed discussion about any hazardous jobs must always be carried out in consultation with the safety officer before the job commences.
A copy of this report should be circulated in the company.
Training needs for all staff on the dangers of entry into enclosed spaces must be reviewed, taking into consideration their level of responsibility on board and experience.
A supply of compressors to recharge SCBA bottles on board should be considered. Ships' staff are reluctant to use SCBA sets for training and for access into enclosed spaces as they fear that the air in the bottles will be used up and not available for emergencies or PSC inspections. Refilling is also difficult at many ports.
All personal safety devices must be suitably labelled to avoid misuse.
Material safety data sheets (MSDS) must be obtained from the shipper prior to any cargo loading.