Introduction
In this section of the Time Pressure Guides you will find information relating to the shipowner/ship manager. The section will detail situations, issues, and subjects to give the reader an understanding of time pressures, specifically in a context of shipowner and/or manager and share recommendations on how to manage them.
The ship owner/manager role (in time pressure)
The shipowner may have several roles with respect to time pressure, use the drop down boxes below to find out more.
Existing time pressure management
Even if there are neither mandatory regulations nor explicit mention of time pressure in the international regulations or requirements ISM envisages the management of a variety of hazards. Companies may have already set up some check balance functions in their organisations which also take up the role of a safeguard from time pressure.
Example, a pre-chartering risk assessment, assesses a potential charter for all the risks and in doing so, time-pressure may also be assessed and if the ship involved will not be able to perform the charter within the given time slot, then it should be either rejected or a different ship assigned to the charter. |
The Master’s overriding authority in matters concerns safety and prevention of pollution, is sometimes used as an effective safeguard to alleviate any extreme time pressure situations.
Example, if a charterer requests a ship to take a shortcut from the planned passage to save time, and where the master assesses it as risking the safety of the ship or environment, he can use his authority to override the instruction. |
It should be stressed that where excessive time pressure originates with or is transmitted by the Company, it is the Company’s role to mitigate that time pressure before instructions are transmitted to the ship thus avoiding the Master being put under pressure.
However, there are also examples where these effective safeguards are not in place or placed incorrectly, or not used correctly or where a safeguard is placed correctly, it has a weakness which leads to problems.
Safeguards
This section of the guide will focus on these safeguards, their use, the potential weaknesses and potential solutions. The aim is to make the reader aware of these issues and take measures to improve them. Where the time pressure originates within the ‘Company’ (as defined in the International Safety Management Code (ISM)), or is transmitted to the vessel by them it is that organisations role and responsibility to minimise the effect of that pressure.
It is self-evident that some form of risk assessment is carried out before a ship is chartered to ensure the ship is fit, in its current condition, for the cargo proposed and that the port is safe for the ship to enter. This assessment should also include the time available for the ship to conduct the needed operations.
Pre-chartering risk assessment, as the name suggests, is an assessment of the risks involved in the charter and gives a chance for the ship-owner to weigh these risks against the pay off and therefore, the pre chartering risk assessment becomes a key barrier in managing time pressures arising out of a charter party. It should be recognised that the decision based on this assessment is critical. This is the last point in the ‘fixing’ process where an unsuitable cargo can be avoided without prejudicing safety or incurring commercial consequences.
A properly carried out risk assessment can mitigate of lot of unwanted outcomes at a later stage, for example, financial risks, legal risks and/or operational risks. Under operational risk, a ship may be delayed to a port or may call a port without properly preparing its cargo holds/tanks etc. However, there can also be instances when such a safeguard does not carry out its intended purpose. Despite knowing that the ship cannot perform the charter without carrying out shortcuts, the charter is accepted as it may seem too lucrative to reject. There could also be other weaknesses which are discussed below.
Potential weaknesses and solutions
Potential Weaknesses |
Solutions |
In an organisation where shipowner, operator and technical managers are different entities, ship-owner pressurises the ship operator on getting the charter, as the deal is lucrative, even if it means taking additional time pressure and this then has the effect of technical managers and ship having to take shortcuts to perform the voyage. Organisational structure of the shipping company where decisions are taken by ship-owner when it comes to business decisions. However, the accountability for safety is passed on the technical managers. Organisational culture of the shipping company is such that decisions are not taken purely based on the results of risk assessment. Pre-chartering risk assessment not conducted correctly. Charterer paying a bonus on getting the job done in a shorter time. |
Leadership - Emphasis should be on long term sustainability of the business rather than short term gains. Organisational structure - Proper systems in place. Those that are accountable for the consequences of the risks taken should be the ones to take the risks. ISM scope - Presently, the ISM covers time pressure in a broad manner. Perhaps, SMS should also cover aspects of employment of a ship and should contain the risk assessments and due diligence that a commercial manager should take when dealing with a potential charterer. Organisation culture - This is an extension of the leadership that shows that the focus is on the culture of the organisation. An example of a pre-chartering risk assessment can be found in the Annex-C. |
Many a times, even if a pre-chartering risk assessment fails to catch a potential high time-pressure voyage, the operational and/or technical departments can spot it.
As per ISM code, shipping companies should have safety management systems in place to assess all operational risks and to have safeguards in place to reduce those risks to a level which is as low as reasonably practical. The safety management system has evolved into a powerful tool for all in the company and this tool can used to address many risks. There have been instances where such risks are spotted and counter measures taken, but there are also a few potential weaknesses which are discussed below.
Potential weaknesses and solutions
Potential weaknesses |
Solutions |
The policies and procedures of a company are mostly sufficient to safeguard against risks of time pressure as well, however, this risk is not explicitly stated in the SMS. Just as human factors play a critical role in every aspect of ship operations, time and the pressures arising from it also do. For this reason, the risk of time pressure should also be part of the SMS and explicitly mentioned whenever and wherever required. When there is no overarching system governing this, it is bound to be misused. Therefore, the weakness in this part can be divided as: Scope of SMS – It is generally believed that ISM and SMS applies to only the ship and the technical management of the company. In the same way, finance and accounting departments are seldom ‘within scope’ of ISM despite their having a significant influence on the resources available for the operation of the ship or indeed the purchase and design of the ship. Structure of the company - Proper structure not in place. The decisions of a commercial department can hardly be challenged by the technical or safety department, creating a moral hazard resulting in conflict between technical and commercial department. The technical department is bound by, and accountable for, the safety and operations of the ship, whereas the chartering/commercial department may be motivated by profitability, especially where chartering bonuses are awarded that relate to ‘utilisation’. The commercial viewpoint may dominate, especially in low freight rate markets, resulting in increased risk especially if there is no commercial consequence to taking on a commercial risk. In some companies, these above-mentioned functions are separated as different legal entities or business units. This kind of structure further opens door for silo working mentality and these issues are exaggerated further. Owner Pressure – Owner’s direct involvement in daily operational of the ship. This can have both positive and negative impacts. There are cases when an owner directly involves in the daily operation of the ship, he/she can see the challenges faced and takes a proactive approach in extending the needed resources for improvement of the system, however, there are times when the opposite happens, and it is these scenarios that turn out to be burdensome on the shipping company. Absence of detailed procedures - There are detailed ship-specific procedures for conducting a particular operation, however, detailed information about the time required to safety complete the operation is not always present. The aspect of time is left to the person responsible for carrying out a task leading to some completing the same task in a lengthy period while others carrying out it in a reasonably quick period of time. It may not be clear which one was correct and if there were any safety shortcuts taken while fulfilling the task. Implementation of systems – While procedures are in place in paper or computer-based, implementation remains a question. Real life implementation of the procedure is quite different from what is stated in the SMS. We have seen that different companies implement the same written procedure in different ways. Differences can also be seen between different ships from the same company. Culture – Organisational culture hampering the process of the effective safeguard. This is where self-induced time pressure originates. The culture of the organisation is such that the employees assume that the allocated tasks must be completed in the allocated time, despite being well aware of the fact that it is very difficult to achieve the necessary results without compromising safety. The practice of challenging back is not existent. |
Reviewing the scope of SMS – Scope of the ISM SMS should include the employment aspects of a ship. Including the commercial, finance and accounting departments will help alleviating time pressure that originates from these places. Reorganisation of company structure -Structure of the company should be such that the goals of the individual departments should be well aligned with the overall company’s goals. Responsibility, authority, and accountability should reside in the same department or very close to each other, so time pressure is not exerted between departments. Where pressures are exerted between departments, matters should be elevated to higher levels within the company to find a solution rather than passing it down within departments and to the ship. An organisation with a flat structure benefit from better communications between departments than a hierarchical one. Time frame included in the procedures – Shipboard procedures for carrying out a task should also include an expected time required to complete the task. This will give a fair idea of the time required to not only the person who is going to do the task but to all involved and will further help in planning other tasks accordingly. Change in leadership and culture - Leaders and ship-owners should realise that a positive drive from them can make all the difference and should work towards it. It is also in their hands to change the organisational culture to be make personnel more interactive and to question an order that is not safe to complete in the given time. |
A further line of defence is the Designated Person Ashore whose role, as per the ISM code, includes:
- providing a link between the company and those on board
- monitoring the safety and pollution aspects of the operation of each ship
- direct access to the highest level of management to raise.
In theory the DPA should have access to the highest level of management within the company and raise issues related to safety and prevention of pollution. However, there are potential weakness in this barrier which is often present in companies.
Potential weaknesses and solutions
Potential weaknesses |
Solutions |
Organisational structure – At times, DPA has conflicting responsibilities, which puts pressure on the ships which he manages. On one hand he should act as the safety ambassador of the ship, while on the other, he is also the operational manager who must ensure that the ship fully performs for the charterer. Here DPA himself forms part of the reason that generates time pressure on a ship. Direct access to the top management is not clearly established or not used in scenarios when it must be used. While in theory, this is one of the fundamental objectives of having a DPA, in practice, there are many instances where this is not the case. In some cases, DPA does not use the access he has for alleviating the time pressure on the ships. There are times when the DPA does not receive enough operational information/communication to allow proactive measures. Sometimes, the flow of information from the ship to a DPA can also be questioned. DPA does not have enough resources available to pay full attention to all ships under his overview. For example, the DPA could be assigned more ships than what he can normally concentrate on, and in this case, he must prioritise the more important tasks leaving room for improvement. DPA not performing the role of a DPA. |
Organisational structure – Having a proper organisational structure without conflicting demands can alleviate a lot of this weakness and strengthen this defence in the context of time pressure but also in the overall context of safety management. Providing clear but also separate line of communication to the topmost part of the management can alleviate a lot of issues from this important safeguard. Resources is another important aspect that can improve the job of a DPA immensely. This can ensure that indirect time pressures and, in some cases, self-induced time pressure are reduced. |
The ISM code has provided the Master with some clear roles and given certain strong authority and in certain cases – an overriding authority. In fact, in the context of ISM, Master is the only person who has an overriding authority when it comes to matters regarding safety of the ship and prevention of pollution. While this safeguard can protect the ship in most instances, weaknesses exist here too.
Potential weaknesses and strengths
Potential Weaknesses | Solutions |
Organisational structure – In the written procedures, the master is given the authority he deserves but when it comes to practical matters, decisions are taken with his/her limited involvement or only involved when it comes to the execution end of the task. Here indirect time pressure plays an important role. When looking at the written procedures, it may seem that Master is given all the required authority, however, the practical operations may paint a different picture. The expectation from the Master is that he runs the ship to keep the charterers happy, even if that means cutting some safety corners. Reward structure - Master is also influenced by the reward structure created by the company. The implicit message here is that “this is what the company wants me to do”. Organisational culture – Rather than questioning the unreasonable task, master passes on the time pressure to his subordinates, thereby negating the existence of this authority. Here the indirect time pressure exerted on him is converted into a direct time pressure by him towards his subordinates. Leadership – Leadership both ashore and on board will have to be investigated. Self-induced pressure - Master simply accepts the unreasonable task in the hope of achieving the results by cutting corners, here self-induced time pressure plays a part. |
Organisation Structure and Culture – Certain organisations are better at implementing clearly what is written in their procedures, while others struggle with it. Carrying out the words in action goes a long way in addressing many of the problems associated with safety and not just time pressure. Reward structure – While reward structure is beneficial to great extent, one should focus on not overdoing it. The reward structure should be carefully planned and executed, in keeping in mind that it does not put the staff in a conflicting position to comply with the safety procedures. Self-induced time pressure - This can be mitigated with more ship-shore staff interactions and inducing the organisational culture of needing to get the job done safely even if it means putting additional time. |
Time pressure may also result from maintenance activities. This can be exacerbated by port rules that limit work which can be carried out alongside or at anchor. This may include; pressuring a ship to sail from drydock before all work is completed and/or testing is completed. This will often be accompanied by an aggressive load port ETA. Limiting time available at anchor to carry out major repairs or surveys and insufficient resources available to carry out planned maintenance.
While this can broadly be classified as part of the safety management system, this is highlighted here as a separate safeguard. Planned maintenance and management systems (PMMS) ensure that ships’ systems and equipment are taken care of and maintained to ensure their continued good operation and longevity.
A well planned and executed PMMS ensures that maintenance intervals are planned that it makes the best use of available resources without putting undue pressure on the personnel involved. However, this safeguard also has its barriers.
Potential weaknesses and solutions
Potential weaknesses |
Solutions |
Cost and PMMS are closely knit together. When the cost of running a ship and good performance of a ship is closely knit together, it can create undue pressure on the personnel involved with it. This sort of pressure can group under indirect time pressure. Here, the maintenance of an equipment is either carried out too quickly or carried out with cheaper parts. This results in having to maintain the system at a higher frequency and probably at a higher cost, but since the cost is spread over time, it is not easily captured in the accounts of the ship. The result is extra workload for the ship’s team in each time period, but a higher bonus for the management team. For example, the fleet superintendent and ship’s management team are not only responsible for the safe running of the ship but also the cost-effectiveness of it. When the cost-effectiveness of running of the ship is linked to the bonus of the employees, there may be instances when this aspect takes a higher priority than safety. When bonus is linked to the key performance indicators of the costs of running a ship, employees tend to lean towards earning a higher buck for themselves than looking at the overall safety of the ship. Ship’s performance of planned maintenance is compared within the company’s fleet of other ships and is linked to the budget allocation of the ship. At times, a ship may not be performing as it should be due to external factors which is not really under its control but is penalised. An example to this is one ship is running a route with a short sea passage and a number of frequent port calls. This adds time pressure on the staff involved and encourages them complete all maintenance tasks in a shorter time to log that all tasks have been completed. At times, this may result in safety shortcuts, and at other times, staff are pressurised to work longer and outside their normal working hours to complete the tasks. Another example to this is that one ship runs is running a route where it is costly to fly in spare parts and service engineers when compared to others which are plying in routes where this is not a challenge. This pushes the ship that is affected to procure local and cheap spares and doing the maintenance themselves, rather than flying in a service engineer. All this leads to safety issues at a later stage. Staff assessment is linked to safety management and completion of tasks in each period of time. |
Having a robust PMS with due regard to the longevity of the ship systems. While it is much easier said than done, delinking cost and PMS or investing in better quality and maintenance products keeping the long-term aspect in mind, has the potential to save money and unwanted repair and maintenance. Taking a careful approach when linking staff bonus to performance bonus can also address the situation. In the same realm, delinking a ship’s performance with a fleet’s performance, when there are certain aspects that are out of the hands of the ship can also add to better performance of the ship. |
Conclusions
Time pressure is a specific safety risk that is not explicitly mentioned or addressed in many shipping companies as our current regulations do not directly and explicitly address this. Time pressure may also be a contributory factor in many accidents or incidents.
Taking a focused approach to this particular risk can go a long way in not only addressing the safe operation of ships but also contribute to better management of company in the long run.
Where to download the guide?
Figures and diagrams
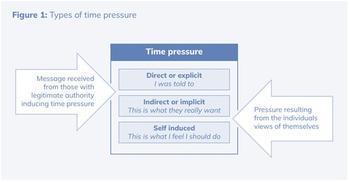
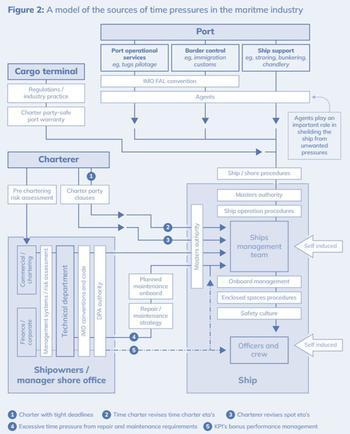
Annex A

Further reading